
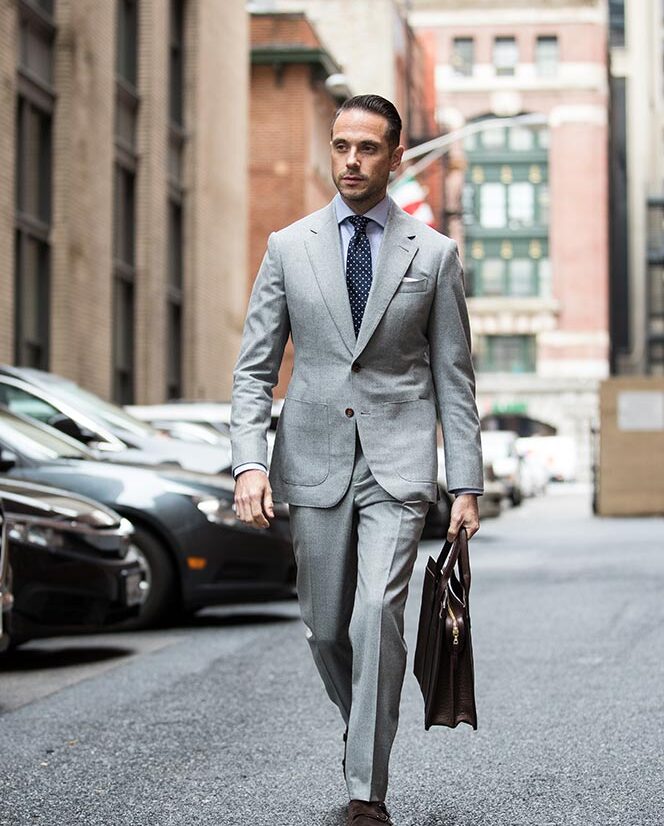
Share
My second suit from Michael Andrews Bespoke deserves a review
There is no shortage of custom suit options in New York City. You’ve got traditional high-end department stores, international menswear chains, national custom suit “brands” and small tailor shops offering a range of affordable options as well as sky-is-the-limit possibilities. I’ve been lucky to have had the opportunity to experience a number of different programs – from the exceptional to the unfortunately not so great. A few months ago, I had the great fortune to work with folks at Michael Andrews Bespoke.
Now, this was not my first Michael Andrews Bespoke suit. Longtime HSS readers will probably have taken note that my brown tweed three-piece is from Michael Andrews Bespoke as well. I purchased that suit a little over three years ago so it was interesting to go through the process with MAB again, especially since during that time period they’ve added a very important step to their fitting process.
That step is a basted fitting. We recently touched on why the basted fitting is one of the most important parts of the bespoke suit making process and I’ll return to that later on in this review. First, however, I want to open up a can of worms I’m sure is on the mind of any potential new Michael Andrews Bespoke customer: is a MAB suit really a bespoke suit?
Is A Michael Andrews Bespoke Suit Really A Bespoke Suit?
It’s a fair question given that bespoke is a term that is often misunderstood and confused as well as bandied about by custom clothing brands preying on their customers’ lack of knowledge.
HSS readers don’t need to be told that true bespoke is a handmade custom garment that has been crafted from a pattern that is unique to the individual for whom it was made. In other words, the pattern is created for you and not a pre-existing pattern that is altered to “fit” you. A point of contention is whether or not bespoke can have some machine finishing. Some who claim to be “purists” say no, while more educated others know that it can.
The fact is that that sentiment itself is a huge misconception – machine work is a part of bespoke today and no legitimate tailor will tell you differently. For the team at MAB, it’s a question of quality. Cory Sylvester, Michael Andrews Bespoke’s Vice President of Operations told me, “Anyone whoever thinks the outseam of a trouser is better finished by hand than by machine isn’t a purist, they’re ignorant.” Cory also adds that the quality of MAB garments meets or exceeds the standards of quality set forth by the Savile Row Bespoke Association.
What Is The Turnaround Time for a Michael Andrews Bespoke suit?
First time clients typically have a turnaround time between eight to 12 weeks. If this seems a little longer than other programs, it’s because a new MAB client won’t have a pattern on file. The sequence of events goes as follows: initial appointment and commission with measuring, a basted fitting three to four weeks later, a first fitting three to four weeks following the basted, a final fitting a week or two later and if there are any subsequent fittings, they’ll take place one week after that.
Returning clients see a bit of an accelerated timeline of six to eight weeks. After commissioning a new garment, the first fitting is four to six weeks and a final fitting one to two weeks after that. Again, any subsequent fittings will happen a week after the final fitting.
| WEARING | Michael Andrews Bespoke suit and shirt, Suitsupply tie and shoes, Frank Clegg briefcase, Rolex watch | PHOTOGRAPHY | by Rob McIver Photo
Where is the pattern made and where is the work actually being done?
Patterns for all MAB clients are created in their New York City studio. Once the pattern is made, the garments are hand cut and sewn by their team of master artisans in a workshop owned and operated by Michael Andrews Bespoke in Shenzhen, China. Following that, the garment is sent back to NYC to be fit and finished on-site by their tailors. Then the fitting process and the finished product.
Okay, but how is the service and experience?
First, let’s talk about the superficial before getting into the nuts and bolts. The MAB studio is very, very cool. You enter through a gate in a small alley off Great Jones – perfect for me as one of my favorite spots, Lafayette Grand, is just around the corner. It’s got a super luxe, relaxing and inviting feel as well as a bar stocked quite well with a fine selection of spirits.
The staff is friendly, knowledgable and passionate. We got on quite well. This is actually something that’s extremely important when it comes to finding the right custom tailor for you – you’ve got to “feel” it with them. I was talking with a friend not too long ago, who works in the custom clothing industry and he told me how he said “no” to a lot of potential employers simply because he didn’t feel like he was a good fit for their culture, personality or aesthetic. So you need to make sure it feels like a good fit before spending money on a suit that you hope will be a good fit.
As I knew exactly what I was in the market for, it didn’t take long for me to go through the process. As you can see, I chose a classic light grey flannel from Scabal – it was the beginning of November – with notch lapels, patch pockets, brown horn buttons, a tone on tone lining and trousers with side adjusters.
Earlier in the review I mentioned that I’d come back to my first MAB suit vs. my second in the context of not having a basted fitting to having a basted fitting. Let’s get into that.
When my brown tweed suit was made, I did not have a basted. And I think it showed. A few aspects of the suit were a little off, which is one reason you probably hadn’t seen it on the site in a while. The shoulders were a little wide, the trouser legs a little wide and the sleeves a little wide. Could these issues have been taken care of in subsequent fittings? Probably. But it wouldn’t have been necessary if I’d had a proper basted fitting. (N.B. During the latest process, I brought my tweed suit in and the Michael Andrews Bespoke team altered it to perfection. Can’t wait until it’s cold enough to wear it again.)
For my grey flannel, the basted definitely helped. I should note that there was a slight fit problem when I came in for my first fitting – mostly the jacket sleeves were quite tight – and the team was horrified and not quite sure what happened, especially since the basted went so well. Needless to say, it didn’t take long for the garment to be recut and shipped back to be fitted again and this time it was pretty spot on, only requiring typical, and very minor alterations.
Throughout the entire process there was a level of care and attention to detail that I really appreciated. There are times when you get into the process of having a suit made, especially if you’re a little indecisive or it isn’t going so smoothly, that you’ll feel the salesperson getting antsy and impatient with you. At Michael Andrews Bespoke, there was nothing but professional vibes and courteous behavior. That goes a long way with me.
Thanks, as always, for reading.
Stylishly Yours,
Brian Sacawa
He Spoke Style